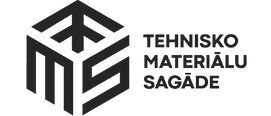
About Us
Manufacturing Process of High-Quality Metal Hoses
At the heart of Europe, in Riga, Latvia, we produce high-performance metal hoses designed for diverse industrial applications. Using state-of-the-art equipment, we manufacture hoses from premium materials, primarily 316L and 321L stainless steel, ensuring exceptional corrosion resistance, durability, and reliability.
Material Selection & Coating: The core material used in our metal hoses is 316L and 321L stainless steel, renowned for their excellent performance in high-pressure environments and aggressive chemical applications. For the outer layer, we apply 304 stainless steel coating, providing an additional layer of protection against wear and tear while also enhancing the aesthetic quality of the hose.
Precision Manufacturing: Our team utilizes cutting-edge manufacturing techniques to form and shape these hoses, ensuring tight tolerances and reliable performance in even the most demanding conditions. Each hose is carefully constructed with the utmost attention to detail to meet our clients’ exact specifications.
Easy Delivery Across Europe: Once production is complete, our products are ready for efficient and fast delivery across Europe. From our Riga facility, we ensure seamless logistics and quick transit times to meet our customers’ needs, no matter the destination.
Our commitment to quality, combined with the ease of delivery throughout Europe, guarantees that our clients receive the best metal hoses, on time, every time.
Here's an overview of the production process:
-
Material Selection:
We use top-grade stainless steel for the construction of our metal hoses:-
316L Stainless Steel: Known for its superior corrosion resistance, particularly in marine, chemical, and high-temperature environments. This material is ideal for applications requiring durability and resilience against aggressive materials.
-
321L Stainless Steel: Offers excellent resistance to oxidation and corrosion in high-temperature environments. Its stabilized titanium content makes it perfect for use in elevated temperature applications where other materials might degrade.
-
304 Stainless Steel (Coating/Outer Layer): The outer layer of the hose is coated with 304 stainless steel, known for its excellent corrosion resistance and formability. This coating enhances the hose's protection against environmental stress while maintaining the structural integrity of the hose.
-
-
Corrugation Forming:
The stainless steel tubing is carefully shaped into precise corrugated patterns. These corrugations are essential for flexibility, allowing the hose to handle dynamic movement and absorb vibrations while retaining its structural strength. The forming process ensures uniformity in wall thickness and accurate corrugation spacing. -
Layering and Coating:
After forming the corrugated tube, the hose is coated with 304 stainless steel. This coating is applied using advanced techniques to ensure a smooth and durable outer layer that provides additional protection against corrosion and wear. The 304 stainless steel coating also serves as a protective barrier against harsh environmental factors. -
End Fittings and Assembly:
The hoses can be equipped with any end fittings, which are precisely welded or crimped to ensure leak-proof seals. The fittings are designed to meet specific industry standards, ensuring compatibility with a wide range of equipment and systems. -
Quality Control and Testing:
Before shipment, each hose undergoes rigorous quality control testing. This includes pressure testing to check for leaks, dimensional inspections to ensure compliance with specifications, and visual assessments to confirm the integrity of the corrugations and coating. We also perform thermal resistance tests to ensure the hose meets the required temperature tolerances. -
Final Inspection and Packaging:
The hoses are then inspected for any defects or inconsistencies. After passing final quality checks, the hoses are carefully packaged for transport. Customization options, such as specific lengths, diameters, and additional features, are provided to meet customer requirements as well as markings on hoses per order
Manufacturing Location
Our metal hoses are proudly produced in Riga, Latvia, located at the very heart of Europe. Latvia’s strong industrial heritage and strategic location allow us to leverage the latest manufacturing technologies and maintain efficient production cycles. By choosing Riga as the manufacturing base, we ensure timely delivery, strict quality control, and a sustainable supply chain that supports our clients across Europe and beyond.
This process ensures that every hose produced meets the highest standards of performance, durability, and flexibility, making them suitable for a wide range of industries, including chemical processing, gas technology, food processing, and more. The use of premium materials, combined with expert production techniques in Riga, guarantees a product that stands the test of time.

Contact Us
Address
SIA "Tehnisko Matriālu Sagāde"
Ramulu street 23,Riga,Latvia LV-1005
Contact
+371 22114858
+371 22114878
Opening Hours
Mon - Fri
9:00 – 17:00
Saturday
-
Sunday
-